Atlantis Foundries automates Core Assembly
As metalcasters contend with a shortage of skilled workers, the requirements for environmental protection and resource conservation, increased quality requirements, and greater emphasis on ergonomics, Atlantis Foundries is expanding its focus on complete automation.
Robotic Innovations uses Fanuc robots for picking and placing as well as core trimming.
Traditionally foundries, whether they are ferrous or non-ferrous, constantly deal with the goal of efficiency, flexibility and work safety. They have to deal with new market requirements, producing an increasingly wide range of products and shorter life cycles, the growing focus on Industry 4.0, sustainability and connectivity with the digital revolution.
With this in mind over six years ago Atlantis Foundries embarked on a process that has paved the way to becoming a Smart Foundry by embracing the Fourth Industrial Revolution. The project, which is continuous, aims to combine various technologies available to gather and analyse process data, with the purpose of improving product quality and cost efficiency.
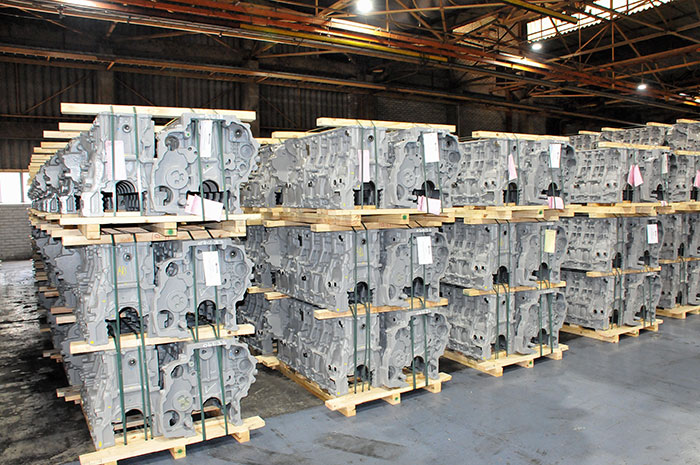
There is a relatively large amount of metal that goes into each product that Atlantis Foundries manufactures – on average 430 kilograms per engine block
The basic building blocks for such a concept are robotics, process instrumentation, and the tracking of components using RFID and other software applications. With all the data available and it being traceable to individual castings, the door has opened to enable the use of Artificial Intelligence for process control and inspection of components.
At the time Pieter du Plessis, CEO of Atlantis Foundries explained: “The corner stone of the project is the programme of automation in the foundry. The Fanuc robots installed by Robotic Innovations have become the workhorse to carry instruments that acquire data while handling or performing its operations. All the data collected throughout the process by the robots and the variety of inline instruments will be linked to specific castings. At the end of the process, the entire set of process parameters, including operator information, will be available for each casting.”
“This process data will be analysed using Artificial Intelligence to predict various aspects of the castings such as material properties and sub-surface defects.”
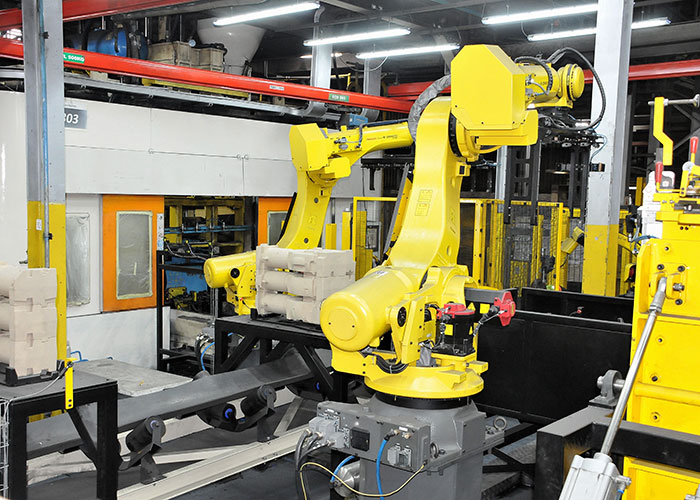
The latest project to be completed at Atlantis Foundries by Robotic Innovations is the automation of core assembly handling
Atlantis Foundries uses cold box technology to facilitate the full spectrum of shapes and sizes across its engine blocks, operating fully automated core dipping facilities to connect to its tunnel indexing core drying oven and using green sand moulding techniques to be able to cast the full range of automotive component grey cast iron grades.
Operational Improvements
A number of processes were implemented during the pandemic to further organise the various areas of the foundry and to streamline the operations. This included purchasing new equipment, as well upgrading and refurbishing existing equipment, and even the installation of radiation portal monitors that detect radioactive sources in trucks tasked with transporting iron and steel scrap to site. This certainty in planning and the rolling out of projects at the foundry has been aided by the reacquisition of the foundry by Daimler Truck AG in 2020.
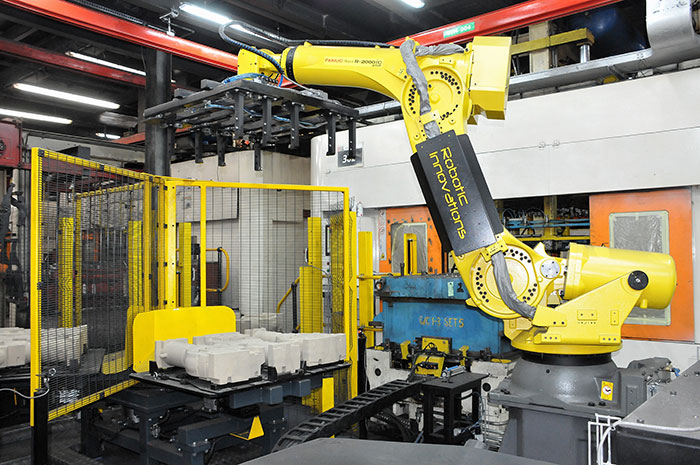
Broadening automation at Atlantis Foundries, Robotic Innovations recently installed seven Fanuc robots – three medium sized Fanuc R2000iC 270kg capacity robots to do the picking and placing, with four Fanuc M10iD 12kg robots performing the core trimming
“There is a relatively large amount of metal that goes into each product that we manufacture – on average 430 kilograms per engine block – so each time we have to scrap one it is very costly, especially if you take into account the complete process, including all the administrative work and the internal and external factors that surround one engine block. Atlantis Foundries export all of their castings to the USA and Europe, and with these long supply lines, any type of failure can be very costly if castings require rework or sorting at the customer.”
Live data
“Our target is to get to the immediacy of live data so that we can react immediately to the analysis that this data provides. At the moment we have about a one-week lag but when you consider the several gigabytes of data, images and other information that are being analysed on a daily basis, we are well down the line.”
“As we all know the foundry process is complex and has many separate steps, with each step having many process variables that influence the quality of castings. Additionally, there are many different material input factors, such as sand and chemistry that can vary from batch to batch or supplier, that need to be taken into account. Metal temperature and pouring time are also contributing factors. All of these parameters, if they are not correctly managed, will impact on our objective of zero-defects.”
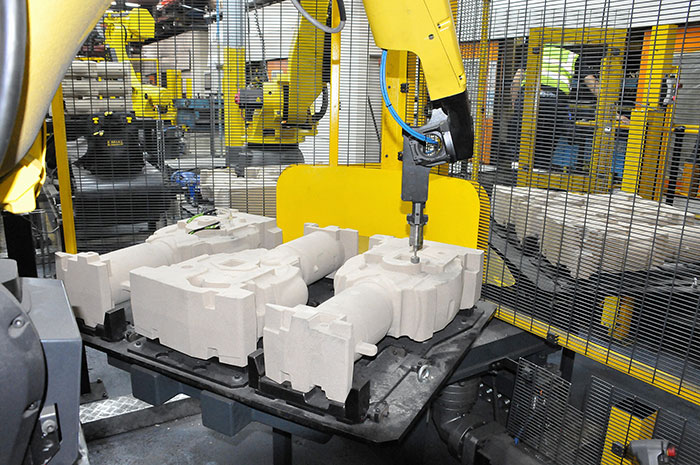
The two core trimming cells at either end of the core shooters consist of two robots, two 120˚ servo indexing turn-tables and one 180˚ forward/backwards indexing turn-table
“As we said previously the corner stone of the project is the programme of automation in the foundry. The Fanuc robots installed by Robotic Innovations have become the workhorses and we have continued to install new robots in various departments in the foundry including sand preparation, core shooting, core transport, core finishing, and in moulding plant automation,” explained du Plessis.
“One of the first and the biggest robots to be installed was a Fanuc M-900iC dipping robot linked with the automatic coating control systems, supplied by Proservice in Italy. You will see that this example set the pattern for the rest of the robot installations where it is feasible to use them. Applications where heavy components or castings are involved and repetitive tasks, aspects where humans can have a big influence on the final product, are the areas that we have targeted for our Fanuc robots.”
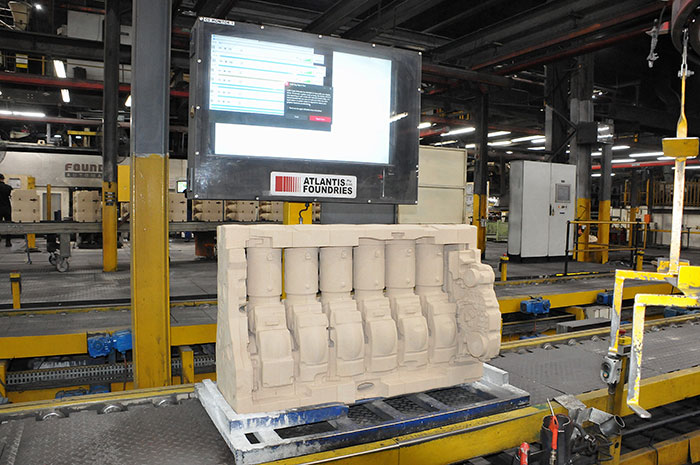
The goal of the project is to automatically stack the eight sand cores that make up the inside of the engine blocks manufactured by Atlantis Foundries
Ingate cutting system
“We want consistency in our processes. For example, our ingate cutting system has a combination of one large Fanuc M900iC 700kg capacity handling robot that loads and unloads the blocks into a positive location jig, so that a smaller Fanuc R2000iC 210F robot fitted with a Fanuc spindle motor and diamond cutting blade can cut the moulding ingates situated on the CAM section of the blocks after moulding.”
“This was a huge win for Atlantis Foundries as the position of the ingates required very heavy grinders within a very tight space to be used manually. A terrible job simplified with great success by using robots, thanks to Robotic Innovations who have been involved with setting up the robots and the programming of them since we installed our first Fanuc robot in 2017.”
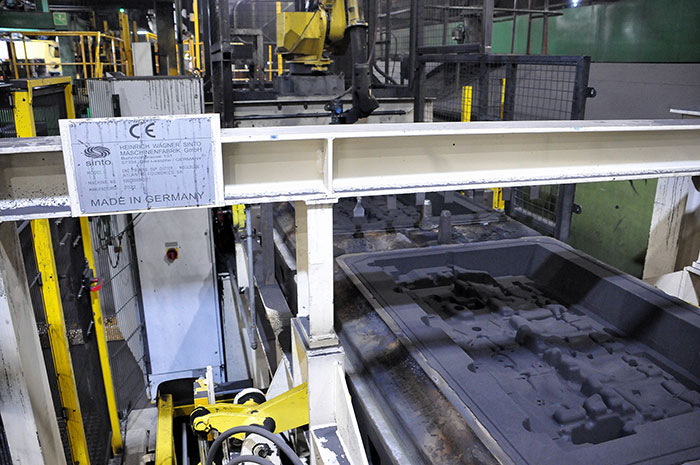
Atlantis Foundries have incorporated a Heinrich Wagner Sinto CNC profile cutter into the moulding line. The HWS mills the sand with rotating blade heads and other tooling along the mould flask
“We – Atlantis Foundries – had a number of top priority projects that we envisaged would enhance our vision of becoming a Smart Foundry, with the underlying objective to improve quality, health and safety and efficiencies. Once a concept has been visualised, we then hand the idea over to Robotic Innovations who project manages each installation and system setup, as they specialise in robotic system integration and design turnkey automation systems for a number of manufacturing applications.”
Some older projects: Mould breather holes and pouring cup cleaning
A Fanuc M-710iC 20L robot uses different nozzles to clean out the breathing holes and pouring cup of the top portion of the main mould.
Fettling training robot
As part of a large future project, Atlantis Foundries invested in fettling training and a R&D robot system that makes use a Fanuc M900iC 700kg capacity robot to load blocks onto jigs using a Fanuc part identification and positioning camera. A smaller Fanuc R2000iC 210kg robot, equipped with a Fanuc spindle motor, is then used to fettle/trim the blocks of excess flash.
“The R&D performed within this cell will equip Atlantis Foundries with the knowledge of what cutting tools and fettling accessories can be used on which portions of the block in order to get the best results when Atlantis Foundries installs automated fettling robot systems in the fettling department in the future,” explained Engineering Manager Mike Hartung.
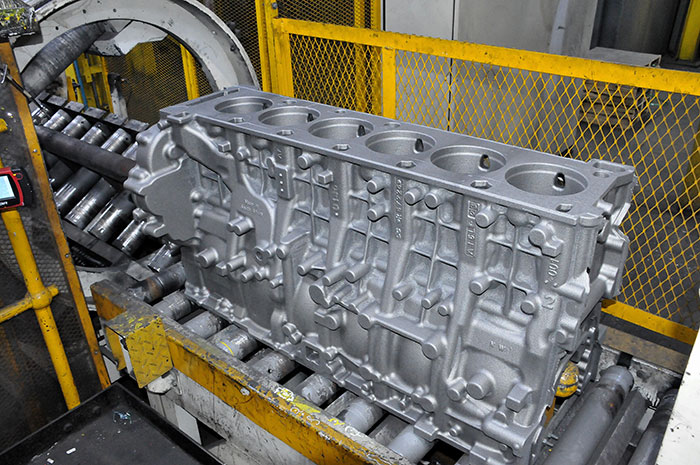
Another new development to aid staff in the inspection department was the installation of a conveyor and turntable system so that manipulation of the on average 430 kilograms per engine block is made easier
“Eight Fanuc robots have been purchased for this future project but in the interim the fettling department bays have been repositioned so as to offer better use of space and the flow of work pieces, better working space for the operators and the easy installation and operation of the robots in future.”
CNC machine loading/unloading system
Besides fettling Atlantis Foundries performs a number of CNC machining operations on the blocks before finishing, such as powder coating, and shipping. Three very large Heller CNC machines make up this department. Before being moved to their current position in the factory the machines operated as individual machines with no work flow and engine block handling had to be negotiated around the fettling department.
“This has now been addressed and the machines have been strategically placed to allow a 12m long robotic linear rail carrying a Fanuc M900iC 700kg capacity robot to run to each machine’s loading/unloading section. Two block infeed conveyors transport the blocks into the cell from where the robot collects them and places them into the correct CNC machine for machining,” continued Hartung.
The same robot collects the machined blocks out of each CNC machine and places them onto an outfeed conveyor. This process was previously performed manually with blocks swinging from KBK overhead cranes. The robot has removed the danger of the operation and implemented control with predictability. Efficiencies have also rocketed and cycle times have been reduced to 90 seconds.
Core printing robot system
Traceability in manufacturing is very important and Atlantis Foundries is on a big drive to reduce scrap which was above industry benchmarks. Thanks to automation, machine and system investment, AI and other improvement investments is scrap rate both internally and externally has become the benchmark.
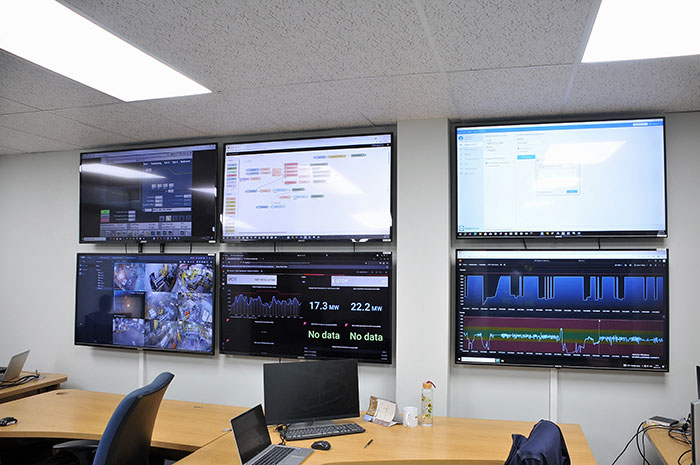
The control room where engineers can monitor all aspects of the plant
Marking the sand cores after they leave the slurry curing oven has been attempted many times without success. Robotic Innovations found the solution in a small Fanuc LR Mate robot fitted with a special industrial ink-jet printer. The trick was finding one that could withstand the dusty environment within the plant.
With experience in the cement palletising industry, Robotic Innovations brought the cement bag date printing technology to the Atlantis Foundries production line.
With data fed from the Atlantis Foundries SCADA control system to the robot and printer, a barcode and matching readable data string is printed onto the core assemblies in a specific position on the core assemblies. This data is then re-confirmed directly after being printed by using the camera which is also mounted onto the robot.
Days later, when each core assembly package is placed within the outer moulds, a camera snaps the barcode and the SCADA system matches the core package to both the upper and lower outer moulds, which in turn is matched to the final product once complete. This is proper manufacturing traceability.
The latest project in the foundry: Core assembly handling
“This project has been in the pipeline for many years and the solution and planning of the installation only started in October of this year,” explained Altus Mostert, Managing Director of Robotic Innovations.
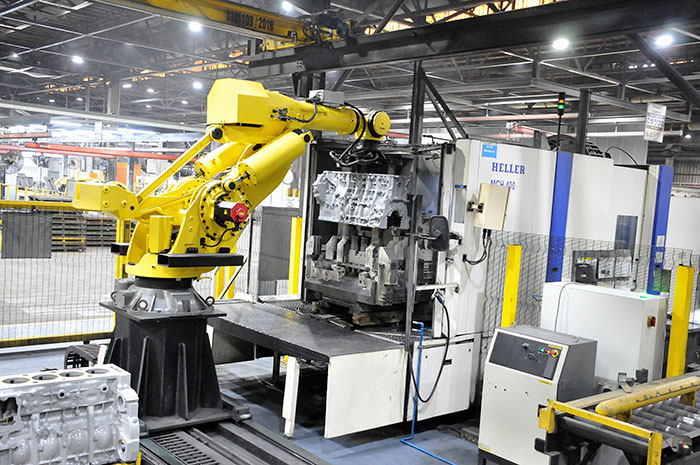
Besides fettling Atlantis Foundries performs a number of CNC machining operations on the blocks, before finishing. Three Heller CNC machines have been strategically placed to allow a 12m long robotic linear rail carrying a Fanuc M900iC 700kg capacity robot to run to each machine’s loading/unloading section. Two block infeed conveyors transport the blocks into the cell from where the robot collects them and places them into the correct CNC machine for machining. The same robot collects the machined blocks out of each CNC machine and places them onto an outfeed conveyor. This process was previously performed manually with blocks swinging from KBK overhead cranes. The robot has removed the danger of the operation and implemented control with predictability. Efficiencies have also rocketed and cycle times have been reduced to 90 seconds
“The goal of the project is to automatically stack the eight sand cores that make up the inside of the engine blocks manufactured by Atlantis Foundries. Easy yes until you have to collect the cores from three very large separate Foundry Automation core shooters, clean each core’s edges of any moulding flash, then they have to undergo an inspection go/reject process, create sequenced sub-assembly stacks and then a final full assembly all to within very strict automotive tolerances and cycle times.”
“Oh yes, I forgot there are two core assembly variants each with three sub-variants with very little to no tooling changeovers being required within the robotic system. Some planning and thinking had to be done over a long period.”
“We used seven Fanuc robots in total. Three medium sized Fanuc R2000iC 270kg capacity robots do the picking and placing with four Fanuc M10iD 12kg robots performing the core trimming. A cell of two robots has been setup at either end of the core shooters and there are two very large 120˚ servo indexing turn-tables and then one even larger 180˚ forward/backwards indexing turn-table. A core reject conveyor and an over/under front and rear core buffering conveyor rounds out the larger pieces of equipment for the system.”
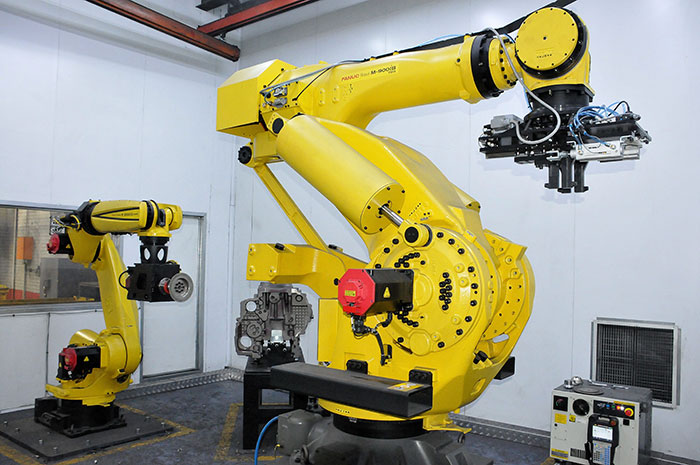
As part of a large future project, Atlantis Foundries invested in fettling training and an R&D robot system that makes use of a Fanuc M900iC 700kg capacity robot to load blocks onto jigs using a Fanuc part identification and positioning camera. A smaller Fanuc R2000iC 210kg robot, equipped with a Fanuc spindle motor, is then used to fettle/trim the blocks of excess flash. “The R&D performed within this cell will equip Atlantis Foundries with the knowledge of what cutting tools and fettling accessories can be used on which portions of the block in order to get the best results when Atlantis Foundries installs automated fettling robot systems in the fettling department in the future,” explained Engineering Manager Mike Hartung
Solar power installation
Earlier this year Atlantis Foundries signed an agreement for a major solar power purchase project. The agreement comprises more than 20 000 solar panels and a total rated capacity of 13.5MWp. The agreement was signed with a long-term power purchase agreement with Energy Partners, an integrated energy solutions company.
According to the terms of the agreement, Energy Partners will engineer, finance, construct and operate the ground-mounted solar energy system at Atlantis Foundries’ production plant. Planning and mapping of the project is now complete and preparing the site has begun. The project is set to commence on 1 May 2024.
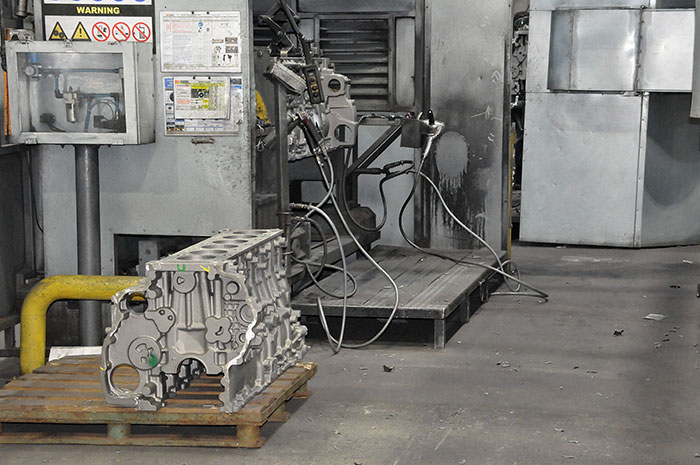
“Eight Fanuc robots have been purchased for this future project but in the interim the fettling department bays have been repositioned so as to offer better use of space and the flow of work pieces, better working space for the operators and the easy installation and operation of the robots in future.”
The system, which has been specifically engineered to align with the foundry’s electrical consumption profile, is estimated to replace up to 20 per cent of Atlantis Foundries’ annual electricity consumption, considerably reducing its carbon footprint and representing a major step towards sustainable energy utilisation.
Generator installation
Another project that has been running concurrently at the Atlantis Foundries site, approximately 50kms north of Cape Town, is the installation of five diesel-powered generators.
“The generators are being installed purely for a precautionary purpose. The first is for if we have a total black-out then we can continue to operate in the foundry and the second is to supplement our power requirements should there be a demand for engine blocks that our current power capacity is not sufficient to meet the demand of.”
“The generators can provide 5MW of power and that is sufficient enough to run the business park that is situated alongside the Atlantis Foundries site.”
Published in December 2023 by Crawford Publications on website: www.castingssa.com